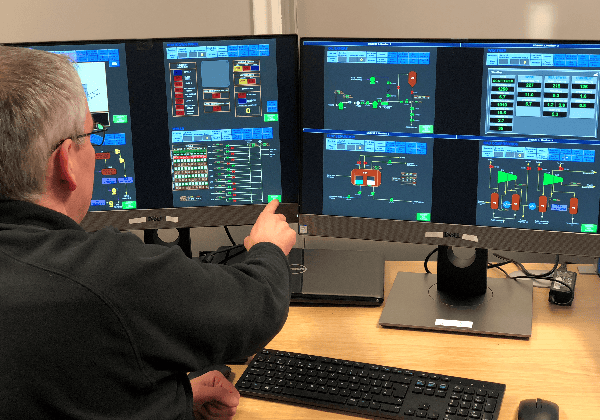
For sheer complexity we think our FPSO simulator is our most realistic and advanced marine model. We combined production, Fire and gas and other key FPSO systems with an incredibly realistic stability and mooring system which allows trainees to experience the full effect of loading, weather and anchor issues on the operation of the vessel, all part of our Operations Training Simulator platform.
We believe that our FPSO model should meet a large range of requirements, however we always welcome the opportunity to create a new model for a specific requirement, designed to whatever level of fidelity meets your needs.
All FPSO models also available online - Train without Travelling.

Features
Pisys can design a bespoke FPSO model to meet your requirements – or we can provide an off-the-shelf model which is widely used to train crews worldwide. Our model is extremely detailed covering all key vessel systems including:
- Tanker offload
- Tank cleaning
- Bilge
- Process alarms/Environmental sounds Stability/Ballast
- Fire & Gas
- Weather
- Water Injection
- Deluge
- Shear forces/Bending moments
- Foam system Multi-phase flow
- Vessel Structure
- Mooring System
- Bilge Management
- Power Generation
- Process Overviews
- Wellhead control
- Water Injection
- Fire & Gas Detection System Fire fighting system
Instructor Control
All our simulators have the facility for an instructor to observe and interact with the trainees.
The instructor can create and run scenarios as well as altering the state of the model. For example a valve which was working normally could be changed to a faulty state, or a smoke detector could be activated.
In the FPSO model the instructor also has access to a full range of mooring scenarios including weather changes, lost anchors etc. The student responses can be recorded and used for later review. There is also a pause/speed function which allows a scenario to be paused for review or advanced to reach a particular state.
An infinite number of ‘scenarios’ can be created for training. These are led by an instructor and can focus on small parts of the system or can combine disciplines for a full exercise. The instructor has the ability to pause or ‘fast forward’ the timeline at any point and the actions of the trainees may be recorded for external assessment by certifying bodies or for internal review.
Here’s an example of training scenarios which can be created:
- Storm condition – combination of wind, wave and current up to one hundred condition and above
- Variation of water density (salt, fresh and aerated water due to subsurface blow out)
- Effects of roll, pitch, heave, surge, sway, yaw and drifting from wellhead
- Pump failure (cargo, ballast, etc.)
- Great inclining angles
- Loading and Oil Storage
- Inert Gas system failures (generator, colling pumps, inert gas seal, blower, vent post, vacuum breaker, etc)
- Black-out
- Failure in emergency generator
- Using the operation manual
- Pump cavitations
- Riser tension variation
- Failure in hydraulic power unit of cargo and ballast pumps (in case of hydraulic pumps)
- Failure in valves of cargo and ballast tanks
- Failure in offloading system (BLS, hawser, hose reel, etc)
- Mooring and subsea layouts
- Stability and Hull Stresses
- Failure in mooring lines
- Drag of anchors
- Damage and flooding of machinery spaces, pump room and wing tanks
- Shuttle Tanker Operations and Offloading
- Preparations for Tank Entry
- Unexpected inclination
- Environmental Protection, Safety Case & Hufids
- Unexpected variation in displacement
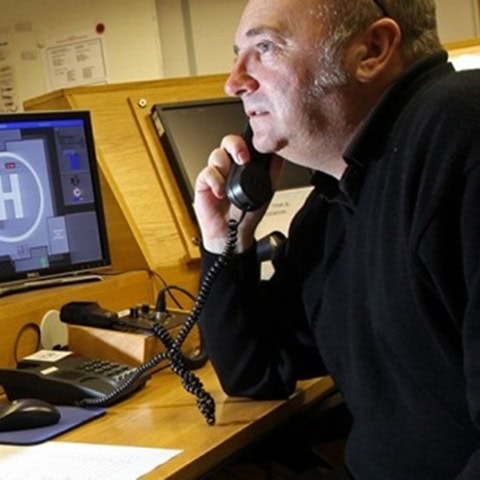
MEM Training
Major emergency management training in an offshore context refers to specialized training programs designed to prepare personnel working on offshore installations, such as drilling rigs, production platforms, FPSO's and wind farms, for effectively managing and responding to major emergencies. These could include fires, explosions, oil or gas leaks, helicopter crashes, structural failures, stability issues, severe weather events, or any other situation that could pose significant risks to personnel, the environment, or the installation itself. Our on-site and cloud-based MEM simulators are world class and form the basis of many OPITO certified courses worldwide.
Got Questions?