Peter Henderson
Permit to work (PTW) systems, also known as Control of Work Systems, are an ideal way to ensure that work is managed correctly and performed safely and efficiently.
There are many types of system from paper and spreadsheets at one end to an electronic permit to work system at the other.
An effective system requires a combination of the right functionality and enforcement of the right process for using it. Without both of these, you are likely to run into difficulties.
Here are some of the problems that we have encountered with unsuitable permit to work systems and a comparison with electronic systems to demonstrate the benefits of using permit to work software in each instance:
Problems With Inadequate Permit To Work Systems
Underqualified Contractors
It is common to find that contractors are not qualified to do the work required or their certification has expired. A lack of qualifications could result in unsafe working practices, potentially causing accidents. Having an out-of-date certification may lead to exposure to legal action if an incident occurs and an investigation reveals that the contractor’s paperwork was not up to date.
Solution:
Using an electronic permit to work system allows contractors to upload their certifications to a contractor management system as part of the permit to work process. The system can send automatic notifications if certificates expire to avoid issues with out-of date certifications. By including required competencies in the initial permit setup it is easy to prevent personnel with expired competencies, or without the correct qualifications being allocated to tasks.
Other Work In Same Area
Sometimes contractors are not aware of other work happening on-site when they arrive, and they discover that the other jobs being performed affect the work planned for them – particularly for tasks in close proximity to each other. This could result in having to cancel a job, with associated costs, or in the worst case, a safety issue arising because of lack of information and awareness of what else is happening in the same space.
Solution:
Implement a permit to work system which clearly identifies the areas in which work is taking place, preferably on a site layout map, so that Simultaneous Operations (SIMOPS) can be quickly identified. In addition you can implement automated checks within the PTW system which will flag potential SIMOPS before work can be scheduled.
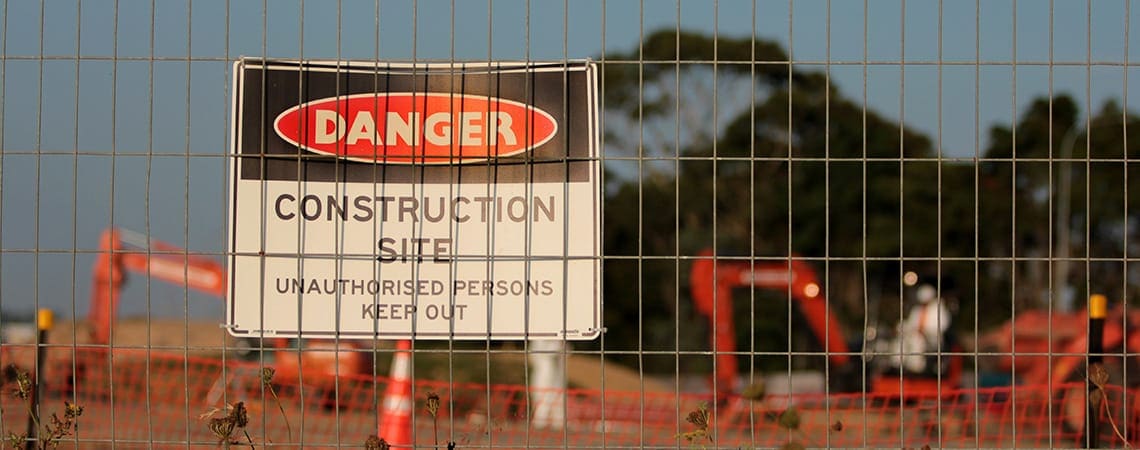
Method Statements Not Available
Method statements provide a clear process for safe task completion. If the correct process is not followed, safety issues may arise, or the job may not be completed to the required standards. If method statements are not available to contractors or can't be accessed by them efficiently, it makes it difficult for them to follow the correct process. The company may also run the risk of commercial or legal exposure should an incident occur.
Solution:
A Permit To Work system should allow storage of method statements, and should prevent permits from being issued if the relevant method statements are not attached. Ideally it should also be possible to create method statements from within the risk assessment process. Using an electronic system makes it easier to create and attach method statements for each task.
Isolations Not In Place
If the required isolations are not in place prior to work starting there are major safety risks. The most direct consequence of inadequate isolation is the heightened risk of accidents, including electrocutions, explosions, and chemical exposures. These incidents can result in severe injuries or fatalities, highlighting the critical importance of proper isolation practices.
Solution:
Your permit to work system should include a dedicated isolations permit which will ensure that all lockout tagout (LOTO) procedures, verification of isolations and safety measures are followed to protect workers.
Gas Tests Not Performed
One of the primary risks associated with inadequate gas testing is the potential for explosions or fires. Flammable gases, if not detected and managed properly, can reach concentrations that are within their explosive or flammable range, leading to catastrophic incidents. There is also the risk that workers may unknowingly be exposed to toxic gases, which can have immediate or long-term health effects. Chronic exposure to certain gases can lead to serious health issues, including respiratory problems, neurological damage, and even death.
Gas testing is crucial for monitoring oxygen levels in the work environment. Oxygen-deficient atmospheres can lead to asphyxiation, while oxygen-enriched environments increase the risk of fires and explosions. Improper gas testing can fail to identify these hazardous conditions, putting workers at risk.
Solution:
A specific Gas Testing Permit should be included as part of any permit to work process, allowing all required data to be logged. Permit activity should not be allowed to proceed until the required data has been entered.
Inadequate Fire Watch
Without a vigilant fire watch, early signs of fire or conditions conducive to fire may go unnoticed until it's too late to prevent or control the fire effectively.
Solution:
Require verification of fire watch as one of the permit questions, and include appropriate competencies for fire watch staff in the list of required worker competencies as part of your permit to work system.
Human Error
It's often the simple things which go wrong when humans are involved in a process - an error in data entry, a lost record or a misplaced permit can cause huge issues.
Solution:
Adopting a digital permit to work system with centralised storage, e.g. a cloud-based system, should reduce the risk of data loss. A digital PTW system also provides opportunities for more effective error checking, data validation and audit. After training, staff should see the system as a benefit whoch will save them time and avoid problems with records going missing.
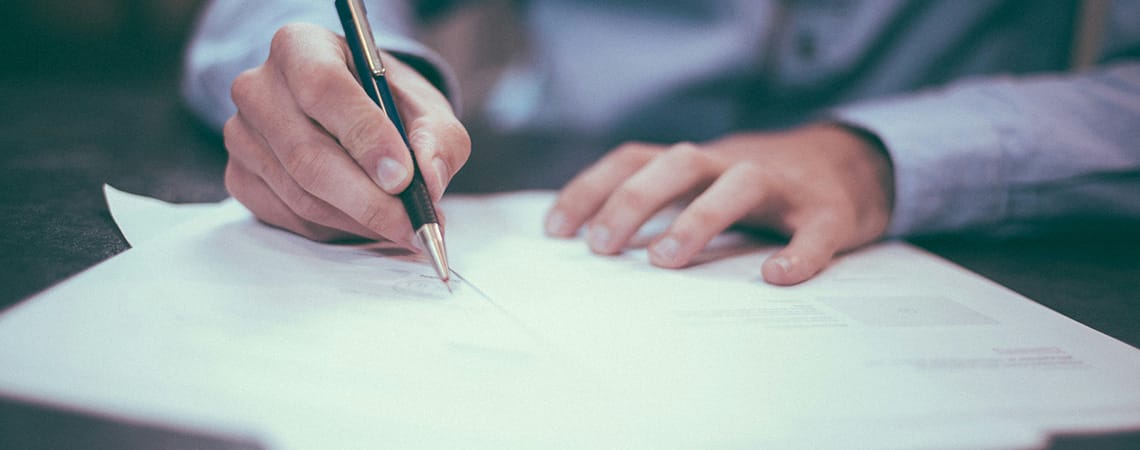
Main Problems With Paper-Based Permit To Work Systems
While many companies still use paper systems to manage their permits, there are several disadvantages involved, and these can lead to increased risk on site if not managed carefully. Moving to custom software can eliminate these disadvantages and make the job safer for your staff and contractors.
Lack Of Flexibility
Paper-based systems require a huge amount of manual input with the opportunity for error at every stage. They can't be viewed and managed remotely, and they often lack the flexibility to accommodate different types of task, which can lead to ad-hoc amendments to forms, potentially causing confusion on-site.
Solution:
Adopting a digital PTW system should allow the configuration of forms to match specific permit requirements. The system should also enforce data entry validation which will reduce errors, providing much greater accuracy.
Too Many Options
If a permit involves multiple activities – e.g. isolations, hot work etc - specific questions must be addressed to ensure that appropriate safety measures and competences are in place. However, in many cases a permit will only need to focus on a subset of these activities. Paper permit forms must by default contain all possible activities, resulting in a cumbersome and potentially confusing form.
Solution:
A digital permit to work system should allow display of permit sections depending on the activities involved, so the permit form changes dynamically, reducing overhead and the potential for error. For example. electronic system permit questions can dynamically change based on simple yes/no answers, so, if hot work is selected a set of questions related to hot work is displayed at that point but is not visible if hot work is not selected.
Time Delays
Because paper forms must be physically moved around for approval/handback etc it is possible that tasks are delayed while waiting for a form to arrive, or, worse, commenced without proper authority due to time delays in processing permits.
Solution:
Central storage of permits allows all relevant stakeholders to have immediate access to data, avoiding unnecessary delays, and controls can be imposed to prevent a permit being issued until all required data has been input and validated.
Hidden Costs
Although a paper-based system can initially appear to be a low-cost option, handling paper incurs a small cost at every stage, principally in the time it takes to physically move the document around, but there is also a less visible cost in the potential errors and omissions which can result from reliance on a paper-based system.
Solution:
A digital PTW system removes the need to physically transport paper around a site, while also helping to reduce errors due to improved data validation, thus saving costs in the long-term.
Difficult To Share Information
There is also an overhead associated with the printing and storage of permits. The fact that paper forms can only exist in one place at a time means that it is difficult to share information, particularly as jobs are happening, since the permit form is likely to be at the job location – this makes it difficult to keep an accurate record of any changes that may occur after the permit has been opened – e.g. changes to the associated risks. Capturing photographic evidence of work done or other job-specific information is difficult or impossible using a paper-based system,
Solution:
A digital PTW system with central permit storage allows data to be shared with all stakeholders at any given moment. Given the prevalence of smartphone cameras an electronic PTW system is a much more convenient solution for the easy sharing of images as everyone involved can quickly take an photo and upload it into the system, giving the entire team visibility of the situation.
As a management aid, the ability to quickly view permits at a specific location should help to identify potential SIMOP issues.

Risk Assessments
Risk assessments and permits often exist as separate paper documents. This can lead to a situation where workers may read the PTW but not refer to the risk assessment—or vice versa. It's often difficult to ensure that everyone is seeing the latest version of the risk assessment - especially when the job is underway and things change. In addition, handwritten forms can be difficult to read and easy to misinterpret!
Solution:
Seamless integration with risk assessment processes should ensure that permits can be raised as part of the risk assessment process, or alternatively, risk assessments can be created as part of the permit issue process and any changes as the job progresses can be easily updated and accessed by authorised staff.
Auditability is also critical in any PTW system. An electronic system will normally store a record of all changes, allowing quick and easy analysis during external audits or investigations.
Quick Checklist - How To Avoid Common Problems With Permit To Work Systems
- Certifications: Implement competency tracking as part of your permit to work system.
- SIMOPS: Ensure that the PTW system clearly identifies the areas in which work is taking place, and can identify potential SIMOPS.
- Method Statements: The PTW system should allow storage and verification of method statements.
- Isolations: The permit to work system should include a dedicated isolations permit module.
- Gas Tests: Include Gas Testing questions as part of the PTW process.
- Fire Watch: Include fire watch competencies and checks as part of the permit to work process.
- Training: Support staff with training on use of systems as well as PTW processes
Implementing a digital permit to work system should bring significant benefits in saved time, reduced errors and improved configuration. If you would like to see how our Permit To Work Software can bring these benefits to your business, please get in touch or request a demo.